Real Impact From Real Solutions
Below are examples of how CREST has partnered with businesses to solve technical challenges, optimize designs & processes, and drive measurable improvements.
Inspired? Let’s discuss what’s possible for your business!
Click Here to Schedule Your FREE Call
Driving $500,000 Annual Savings Through Heart Valve Design Optimization
Client:
Edwards Lifesciences – Large global medical corporation specializing in heart valve therapies
Problem:
The next generation of the PASCAL Heart Valve implant was costly to produce and still required next-gen features to be designed, developed, & delivered… all within an accelerated timeline.
Services Provided:
- Solution Brainstorming
- Design Optimization

Results:
- Streamlined implant design, driving $400/implant savings, totaling approximately $500,000/yr
- Combined two cloth components into one, eliminating a joining stitch-line operation
- Redesigned two component ends to join via a snap-fit, eliminating suture preparation, needle prep, and the associated time-consuming sewing & knot-tying steps
- Reduced total stitch count during implant assembly by over 50%, from more than 300 stitches to fewer than 150, without compromising implant integrity
- Created a Design-for-Manufacturing (DFM) Scorecard to guide future design decisions. Scorecard metrics included:
- Number of Parts
- Material Cost
- Production Yield
- Labor Time
- Training Time
- Unique Metric – Number of stitches
- Instilled a lasting DFM culture within the engineering team
Saved $500,000/yr
Reduced # of Parts
Reduced Assembly Time
Instilled DFM Culture

Enhancing End-User Experience in Cardiac Catheter Systems
Client:
Adagio Medical – Small start-up developing cardiac cryoablation catheter systems
Problem:
The catheter design was difficult for physicians to use and created potential safety risks during navigation within the heart
Services Provided:
- Design Optimization for Product & Services
Results:
- Redesigned the shaped wire geometry to enable smoother, more precise catheter positioning within the heart, improving access to ablation sites
- Improved the shaped wire manufacturing process for greater consistency and reliability, ensuring the catheter shape matched the intended design for optimal navigation
- Re-engineered the stiff catheter connection hose to significantly improve flexibility and operator control, directly addressing physician feedback about “fighting the catheter” and greatly improving overall catheter maneuverability
- Enhanced patient safety by including additional audio feedback:
- Added a tone to confirm safe depressurization and re-pressurization of the catheter
- Added audible beeps to signal when the catheter returned to a safe repositioning temperature, helping prevent patient harm
Improved Ease of Use
Addressed Physician Feedback
Enhanced Patient Safety
Redesigning Catheter to Resolve Low-Flow Issues & Restore Cryoablation Performance
Client:
Adagio Medical – Small start-up developing cardiac cryoablation catheter systems
Problem:
Low cryogenic flow in cryoablation catheters was preventing proper cardiac tissue freezing, leading to ineffective heart ablation procedures.
Services Provided:
- Technical Root Cause Analysis
- Solution Development & Implementation


Results:
- Conducted in-depth testing guided by root cause analysis tools to identify & eliminate the true causes of low flow:
- Root Cause: Inadequate catheter kink resistance
Solution: Updated catheter design & manufacturing process to assemble internal tubes in a tight spiral, creating a kink-resistant coil structure - Root Cause: Poorly designed internal tube structure with sharp U-turns that kinked during assembly
Solution: Redesigned internal tube paths to allow larger, smoother U-turns, eliminating tube kinds without increasing catheter size, and vastly increasing flow cross-sectional area - Root Cause: Shaped wires manufactured with overly tight bends that induced catheter kinks
Solution: Improved wire manufacturing & inspection processes to eliminate low-flow-inducing tight bends
- Root Cause: Inadequate catheter kink resistance
- Delivered the following value-added improvements:
- More than doubled catheter flow from 30 SLPM to 80 SLPM (standard liters per minute)
- Saved over $180,000/yr in scrapped low-flow catheters
- Restored catheter performance critical for effective cryoablation procedures
Doubled Catheter Flow
Saved $180,000/yr
Restored Catheter Performance
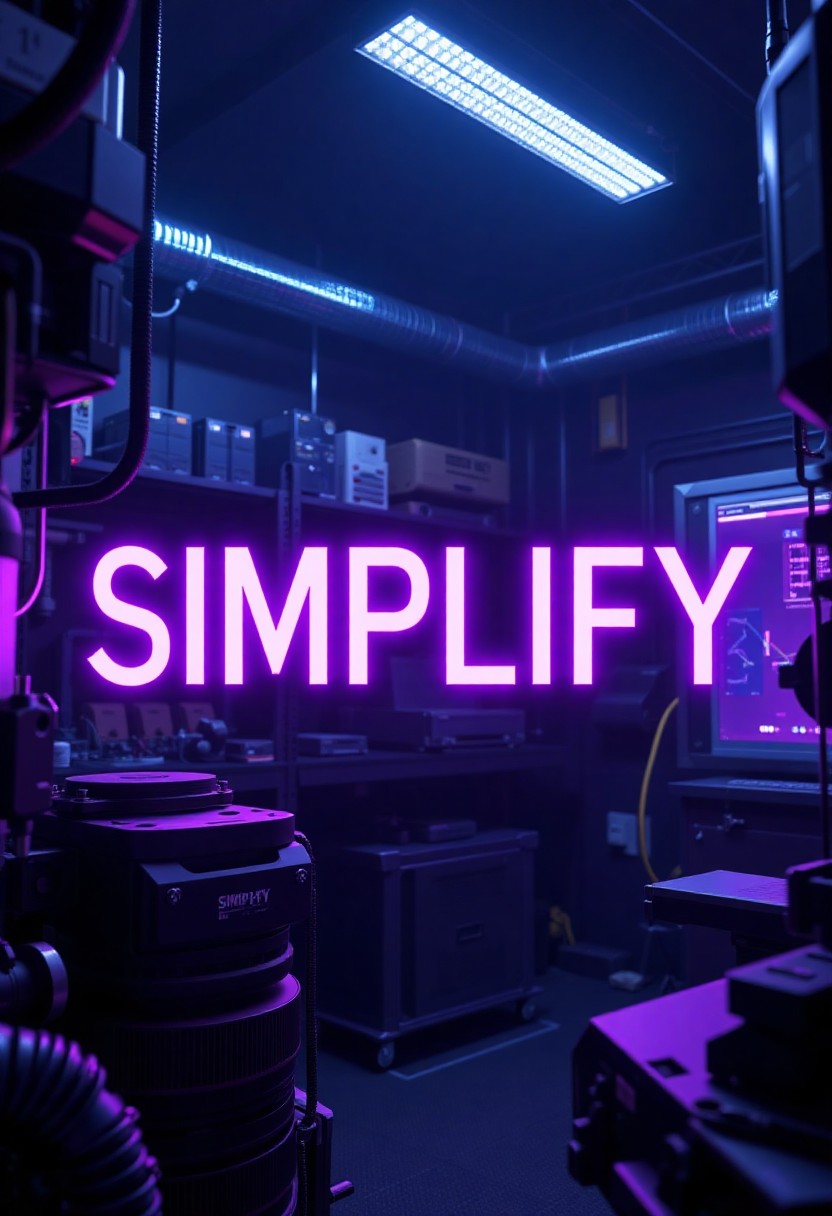
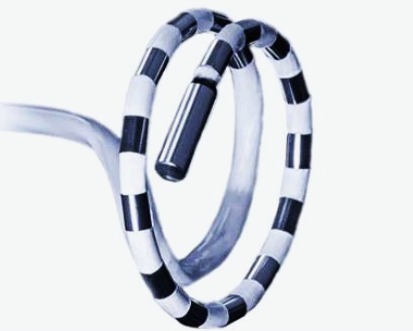
Simplifying Catheter Design to Save $300,000 Annually
Client:
Adagio Medical – Small start-up developing cardiac cryoablation catheter systems
Problem:
Manufacturing costs too high and assembly processes too inefficient, requiring improvements without compromising catheter quality
Services Provided:
- Design Optimization for Product & Services
Results:
- Identified costly component that had become unnecessary after several design iterations, but still used four times per device.
- Eliminated costly component, leading to an estimated $300,000 in annual savings
- Reduced overall assembly time by simplifying the build process through component removal.
- Maintained high product quality standards, ensuring no loss in catheter performance despite cost and complexity reductions
Saved $300,000/yr
Reduced # of Parts
Reduced Assembly Time
Maintained Catheter Quality
Protecting Product Quality: Solving Metal Discoloration and Saving $90,000 Annually
Client:
Inari Medical – Mid-size growing medical device company specializing in venous therapies
Problem:
Yellow discoloration appeared during metal heat treatment, creating quality concerns and significant production scrap
Services Provided:
- Process Optimization for Products & Services
- Technical Root Cause Analysis

Results:
- Confirmed through functional testing that discoloration did not affect product performance, enabling short-term acceptance of parts
- Traced root cause to an argon gas leak in one of four heat treatment ovens
- Redesigned custom oven-to-argon line interface to eliminate leaks and oxidation issues
- Eliminated major recurring production scrap, driving $90,000+ annual savings by preserving hundreds of critical assemblies
Saved $90,000/yr
Redesigned Custom Interface
Eliminated Argon Leak
Eliminated Production Scrap

Driving Smart Decisions Through Real-Time Defect Tracking
Client:
Stryker – A large medical technology company
Problem:
No effective system existed to track defects and their associated costs across the manufacturing plant at one of Stryker’s subsidiaries, Inari Medical
Services Provided:
- Data Tracking Development & Deployment
- Statistical Data Analysis
Results:
- Developed automated defect and cost pareto charts to enable real-time performance tracking across production
- Empowered engineering teams to prioritize high-impact projects based on data-driven insights
- Improved visibility into manufacturing inefficiencies, allowing for smarter resource allocation and more targeted corrective actions
Developed Defect & Cost Pareto
Prioritized Engineering Projects
Allocated Resources Smartly
★★★★★
CREST has transformed our operations with their innovative solutions. Their expertise in engineering consulting has streamlined our processes, leading to significant cost savings and improved efficiency. I highly recommend their services to any business looking to enhance their performance and tackle complex challenges effectively.
Abigail Walker
Engineering Solutions Inc.